We are not the biggest, but we try our hardest. Complaints, should they occur, are handled by us in advance, which is why we have higher quality standards. We don't under-specify small jobs. Thanks to long-term relationships with suppliers and customers and our own development, we have excellent operating economics and therefore unbeatable prices.
Combining craft with technology
CNC metal processing, powder coating, welding, assembly and not only that we can realize with metal of all types and sizes.
Get to know us-
Robotic welding
The robots are able to quickly and consistently produce accurate and high quality welds, which is particularly advantageous for repetitive welding operations.Our welding robot is equipped with the latest MoTion Weld technology for welding and brazing very thin sheet metal using MIG/MAG and TIG/WIG methods.
More information -
Laser Cutting
Cutting technology that enables precise cutting of metals and other materials to size. Thanks to our advanced laser technology, we can economically and quickly produce sheet metal elements to any design, even in small quantities.
More information -
Powder Coating
Powder coating is a process that protects conductive materials such as steel and aluminium from corrosion and wear over the long term. Unlike traditional wet painting, powder coating is faster, more economical, more durable and more environmentally friendly.
More information
Take a look at how we operate
Check out our video showing footage of the production process. Specifically, it is footage from the NORDSON powder coating line.
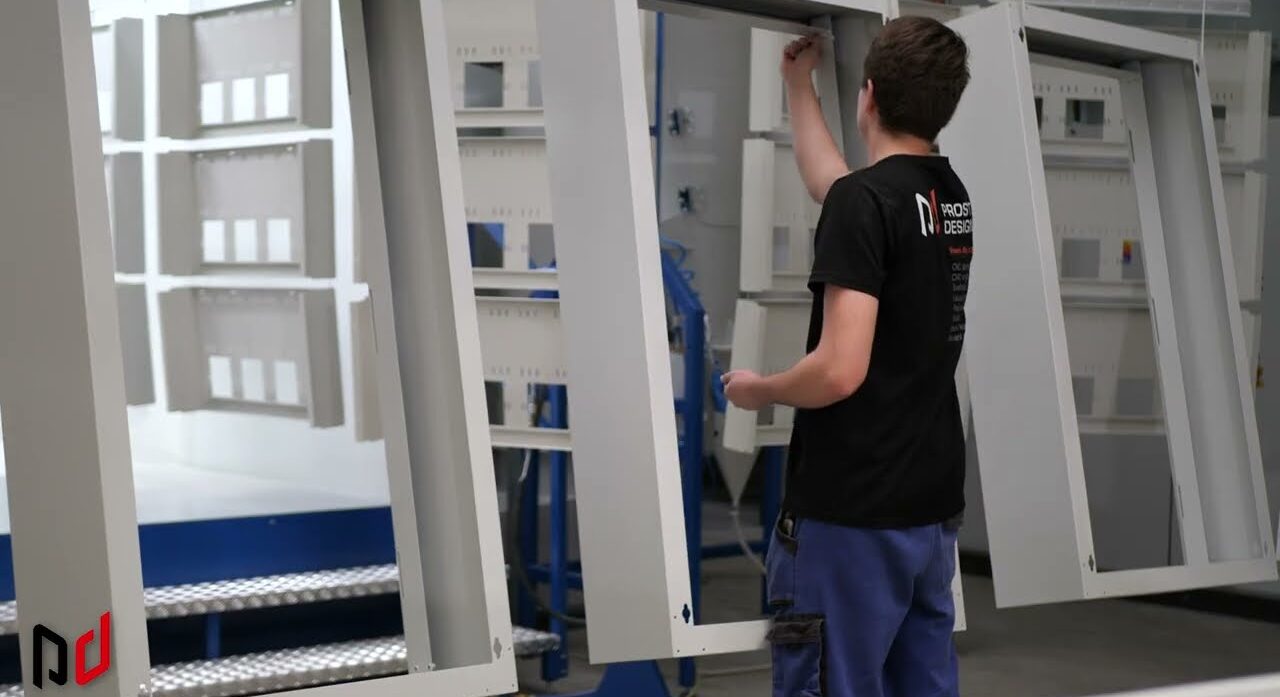
ATTENTION TO DETAIL, PROFESSIONALISM AND 20 YEARS OF EXPERIENCE
We offer sufficient production and warehouse capacity, perfect logistics, and the possibility of Kanban supply. We use the most modern technologies of today - Trumpf, Fronius, Wagner, Hilti or Bosch. With us, you have the goods on the agreed date, where you say and in quality without compromise.
-
Professionalism
-
History
-
Technology
We are a modern European company and our goal is to find solutions for your personal and corporate success.
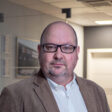
Pavel Gelnar
CEO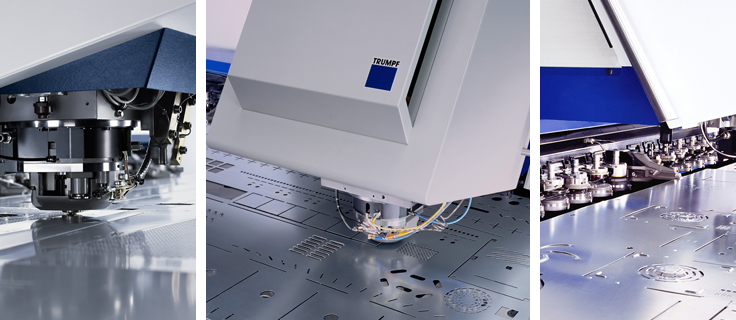
Let's start something new
Contact us and let's start working on your new project!
Contact form
Are you interested in our services? Write to us and leave the rest to us...
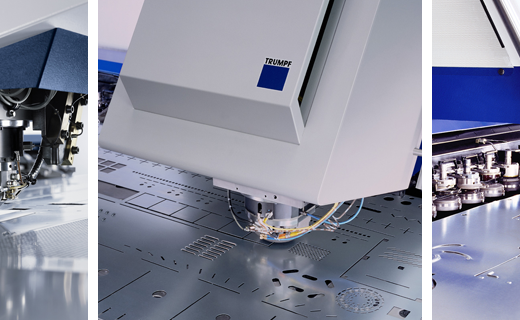